Introduction
In the highly competitive world of manufacturing, understanding and managing costs is critical. One significant but often overlooked area is the Cost of Quality (CoQ). This blog post aims to explain the concept of CoQ, highlight its importance, and provide a detailed methodology for its calculation, complete with a sample scenario.
What is the Cost of Quality?
The Cost of Quality refers to the total cost associated with ensuring products meet quality standards, as well as the cost incurred when products fail to meet these standards
Importance of Knowing the Cost of Quality
Understanding CoQ is crucial for several reasons:
- Improved Decision Making: By identifying and quantifying quality-related costs, companies can make informed decisions about where to invest in quality improvements.
- Cost Reduction: Highlighting the costs associated with poor quality can drive initiatives to reduce failures and improve processes, leading to overall cost savings.
- Customer Satisfaction: Reducing defects and improving quality can enhance customer satisfaction and loyalty.
- Competitive Advantage: Companies that effectively manage their CoQ can gain a competitive edge by offering higher-quality products at lower prices.
Four categories of Cost of Quality
CoQ is typically divided into four categories:
- Prevention Costs
- Appraisal Costs
- Internal Failure Costs
- External Failure Costs
Prevention Costs
Costs incurred to prevent defects and ensure quality standards are met from the beginning. These proactive measures aim to eliminate the potential for errors in the production process.
Examples for Prevention Costs: Training programs for employees, Quality planning and administration, Process control and improvement activities, Supplier quality assurance, Preventive maintenance of equipment
Tips for collecting and organizing data for prevention costs
- Training Programs: Track expenses related to quality training sessions, including trainer fees, materials, and employee time spent in training.
- Quality Planning: Include costs for developing quality management systems, manuals, and procedures.
- Process Control: Document expenses for activities like statistical process control, design of experiments, and quality engineering.
- Supplier Quality: Account for the costs of supplier audits, qualification processes, and collaboration on quality improvement.
- Maintenance: Record the costs of scheduled preventive maintenance activities, including labor, parts, and downtime.
Appraisal Costs
Apprasial costs can be defined as costs that are associated with measuring, evaluating, and auditing products or services to ensure quality standards are met.
Examples for appraisal costs: Inspection and testing of incoming materials, in-process goods, and finished products, Quality audits and assessments, Calibration and maintenance of testing equipment, Field testing and customer surveys.
Tips for collecting and organizing data for apprasial costs
- Inspection and Testing: Keep records of costs for inspection equipment, inspector salaries, and testing supplies.
- Audits: Document costs for internal and external quality audits, including auditor fees, travel expenses, and report generation.
- Calibration: Track expenses for calibrating and maintaining measurement instruments.
- Customer Feedback: Include costs for conducting customer surveys, analyzing feedback, and implementing necessary changes.
Internal Failure Costs
Internal Failure costs result from defects detected before the product or service reaches the customer. These costs arise from rework, scrap, and other corrective measures taken within the organization.
Examples for internal failure costs are: Scrap and rework costs, costs of re-inspection and re-testing, downtime due to quality issues, disposal of defective products, cost of corrective actions.
Tips for collecting and organizing data for Internal failure costs:
- Scrap and Rework: Record the value of scrapped materials and the labor and materials used for rework.
- Re-Inspection: Track costs associated with additional inspection and testing of reworked products.
- Downtime: Document the impact of downtime, including lost production time and associated labor costs.
- Disposal: Record costs related to the disposal of defective products, including transportation and handling fees.
- Corrective Actions: Include costs for root cause analysis, corrective action implementation, and follow-up evaluations.
External Failure Costs
External failure costs are incurred when defects are detected after the product or service has been delivered to the customer. These costs can significantly impact customer satisfaction and the company’s reputation.
Examples for external failure costs are: warranty claims and repairs, product recalls, customer returns and replacements, loss of sales due to dissatisfied customers, legal costs from lawsuits, cost of handling customer complaints.
Tips for collecting and organizing data for external failure costs:
- Warranty and Repairs: Document expenses for warranty claims, repair services, replacement parts, and labor.
- Recalls: Track costs associated with product recalls, including communication, logistics, and replacement products.
- Returns: Record costs related to processing customer returns, including restocking and shipping fees.
- Lost Sales: Estimate the financial impact of lost sales due to poor product quality and negative customer feedback.
- Legal Costs: Include legal fees, settlement costs, and any penalties associated with quality-related lawsuits.
- Complaint Handling: Track costs for managing customer complaints, including call center operations, refunds, and customer service interventions.
Organizing and Presenting Data
You may follow these steps to generate a satisfying CoQ methodology for your organization:
- Create a CoQ Framework:
- Develop a standardized template for collecting CoQ data.
- Ensure all relevant departments (e.g., production, quality, finance) understand the framework and their roles in data collection.
- Data Collection Methods:
- Use existing financial and operational records to gather data.
- Implement specific tracking mechanisms if necessary, such as time logs for rework or detailed records for training expenses.
- Categorize Costs:
- Allocate collected data into the four CoQ categories.
- Use cost centers or specific accounting codes to streamline this process.
- Analyze and Report:
- Summarize the total costs for each category.
- Present the data in a clear, concise format (e.g., tables, graphs).
- Highlight trends and identify areas for improvement.
- Regular Monitoring:
- Establish a routine for periodic CoQ analysis (e.g., monthly, quarterly).
- Use the findings to guide continuous improvement initiatives and strategic decisions.
Calculation Logic
Calculating the Cost of Quality involves several steps:
- Identify Quality-Related Activities: List all activities related to prevention, appraisal, and failure (both internal and external).
- Collect Data: Gather financial data associated with each activity. This can include direct costs (e.g., materials, labor) and indirect costs (e.g., overhead, lost sales).
- Categorize Costs: Classify the costs into prevention, appraisal, internal failure, and external failure categories.
- Sum Costs: Add up the costs in each category to get the total CoQ.
Example Calculation:
Let’s consider a sample scenario to illustrate the calculation:
Scenario:
A manufacturing company produces 10,000 units of a product per month. The following costs are identified:
Prevention Costs | $5,000 | Training programs, quality planning |
Appraisal Costs | $3,000 | Inspection, testing |
Internal Failure Costs | $2,000 | Rework, scrap |
External Failure Costs | $4,000 | Returns, warranty claims |
Calculation:
Total CoQ = Prevention Costs + Appraisal Costs + Internal Failure Costs + External Failure Costs
Total CoQ = $5,000 + $3,000 + $2,000 + $4,000 = $14,000
CoQ per Unit = Total CoQ / Number of Units
CoQ per Unit = $14,000 / 10,000 = $1.40
This means that the cost of quality for the company is $1.40 per unit produced.
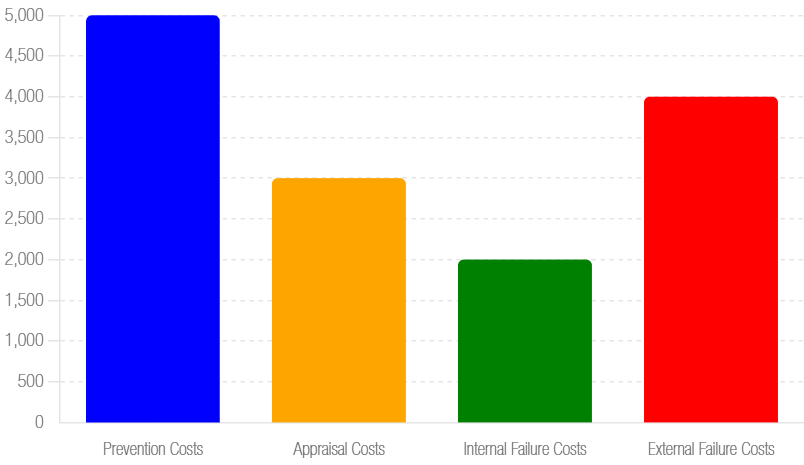
Calculating the Cost of Quality provides valuable insights into the efficiency of quality management systems within manufacturing companies. By understanding and managing CoQ, companies can reduce waste, improve product quality, enhance customer satisfaction, and achieve a competitive advantage in the market. Implementing a robust CoQ calculation and monitoring system is an investment that pays dividends in the long run.
Download Our Free CoQ Calculation Template!
Optimize your manufacturing processes and reduce costs with our comprehensive Cost of Quality (CoQ) Calculation Template. This detailed tool helps you track, analyze, and manage quality-related expenses across various categories. With built-in formulas, sample data, and visual charts, you can easily identify cost-saving opportunities and improve your quality management system. Don’t miss out on this essential resource—download it now and take the first step towards superior quality and efficiency!
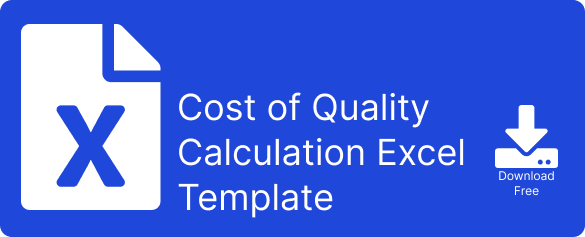
References
- Crosby, P. B. (1979). Quality is Free.
- Juran, J. M., & Gryna, F. M. (1988). Juran’s Quality Control Handbook.
- International Organization for Standardization (ISO). (2023). ISO 9001:2015 Quality Management Systems.